In the dynamic landscape of modern manufacturing, the integration of cobots (collaborative robots) has emerged as a game-changer, revolutionizing production processes and driving efficiency. This article aims to delve into the multifaceted applications of cobots across various industries, exploring their role in enhancing productivity, quality control, and flexibility on the factory floor.
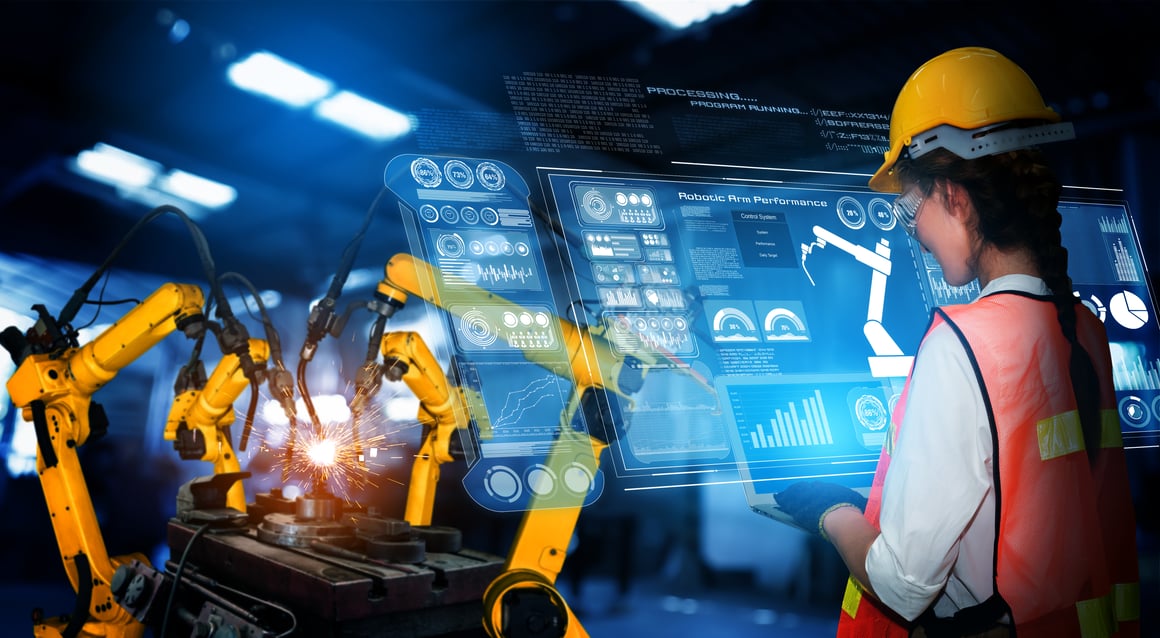
Understanding Cobots: Versatile Collaborators in Manufacturing
Cobots represent a new generation of robots designed to collaborate with human workers in shared workspaces. Unlike traditional industrial robots, cobots are equipped with advanced sensors and safety features, enabling safe and efficient human-robot interaction. Their significance lies in their ability to augment human capabilities, streamline operations, and adapt to changing production needs.
Key Components and Functionalities
Cobots comprise a range of components and functionalities, including sensors, grippers, mobility features, and intuitive programming interfaces. These components enable cobots to perform a variety of tasks, from assembly and quality control to material handling and logistics, with precision and efficiency.
Cobots in Assembly and Production Lines
Cobots play a pivotal role in assembly processes, performing tasks such as pick-and-place operations, component insertion, and product assembly. Their flexibility and adaptability make them ideal for handling diverse components and accommodating changes in production requirements.
Integration into Production Lines
Integrating cobots into production lines enhances efficiency and flexibility, enabling seamless collaboration between human workers and robots. Cobots can work alongside human operators, automating repetitive tasks and allowing workers to focus on more complex and value-added activities.
Enhancing Quality Control with Cobots
Cobots are equipped with advanced vision systems and sensors, enabling precise inspection and quality assurance tasks. They can detect defects, measure dimensions, and perform other quality control checks with accuracy and repeatability.
Real-time Data Analysis
Cobots facilitate real-time data analysis and feedback mechanisms, allowing manufacturers to identify and address quality issues promptly. By monitoring production processes and analyzing data, cobots help maintain consistency and adherence to quality standards.
Cobots in Material Handling and Logistics
Cobots are increasingly being used for material handling tasks, including palletizing, sorting, packaging, and order fulfillment. Their agility and versatility enable them to adapt to changing inventory requirements and optimize warehouse operations.
Integration with Autonomous Systems
Cobots can be integrated with autonomous mobile platforms and flexible parts feeding systems to create efficient and adaptable material handling solutions. These systems enable seamless movement of materials within the manufacturing facility, reducing cycle times and improving throughput.
The Role of Cobots in Flexible Parts Feeding Systems
Flexible parts feeding systems are critical components of automated manufacturing processes, providing a steady supply of components to assembly lines. Cobots play a key role in these systems, facilitating efficient and reliable component delivery. Explore innovative solutions like the Flexibowl to enhance your automated manufacturing processes.
Advantages of Cobot-Assisted Parts Feeding
Cobot-assisted parts feeding systems offer numerous advantages, including reduced setup times, increased flexibility, and improved changeover efficiency. Cobots can adapt to different part sizes and geometries, minimizing downtime and maximizing productivity.
Collaborative Workspaces: Cobots and Human Operators
Designing collaborative workspaces requires careful consideration of safety, ergonomics, and workflow efficiency. Manufacturers must implement appropriate safety features and protocols to ensure safe human-cobot interaction and minimize the risk of accidents or injuries.
Training and education initiatives are essential for promoting effective collaboration between human operators and cobots. Workers need to be trained in cobot operation, maintenance, and safety procedures to maximize productivity and ensure a positive work environment.
Advancements in Cobots and Future Trends
Advancements in cobot technology, including artificial intelligence (AI) and machine learning, are driving innovation and expanding the capabilities of cobots. AI-powered cobots can adapt to dynamic environments, learn from experience, and optimize production processes autonomously.
Future trends in cobot integration include the adoption of predictive maintenance algorithms, the development of collaborative robots with advanced sensing capabilities, and the expansion of cobot applications into new industries and sectors.
Conclusion: Embracing the Potential of Cobots in Manufacturing
In conclusion, cobots represent a paradigm shift in modern manufacturing, offering unparalleled flexibility, efficiency, and safety in production environments. By leveraging the diverse applications of cobots, manufacturers can unlock new opportunities for innovation, productivity, and competitiveness. Embrace the potential of cobots and embark on a journey of transformation in manufacturing.